全球制造业格局正在发生巨变。传统的装配线曾经依赖于手工劳动和孤立的机器,如今正在演变为相互关联的智能生态系统。这种转变的驱动力是 工业 4.0自动化不仅是指自动化,而是指创建能够学习、适应和创新的自我优化系统。这场革命的核心是三大关键技术支柱: 聪慧 连通性, 边缘动力智能和 数据驱动的自治.这些支柱共同弥补了 "制造 "与 "智能制造 "之间的差距,使制造商能够实现前所未有的效率、灵活性和可持续性。
本文探讨了这些技术如何融合在一起,重新定义现代制造业,为准备迎接未来的企业提供可行的见解。
目录
传统制造业面临的挑战
在深入研究解决方案之前,有必要了解阻碍传统工厂发展的限制因素:
- 支离破碎的系统:机器、传感器和软件往往各自为政,造成数据瓶颈。
- 反应式维护:设备故障会导致代价高昂的计划外停机。
- 适应能力有限:僵化的生产线难以适应定制订单或快速的设计变更。
- 能源效率低下:资源利用率低会增加成本和环境影响。
这些挑战要求我们采取全面的方法--将最先进的技术整合到运营的每一个层面。
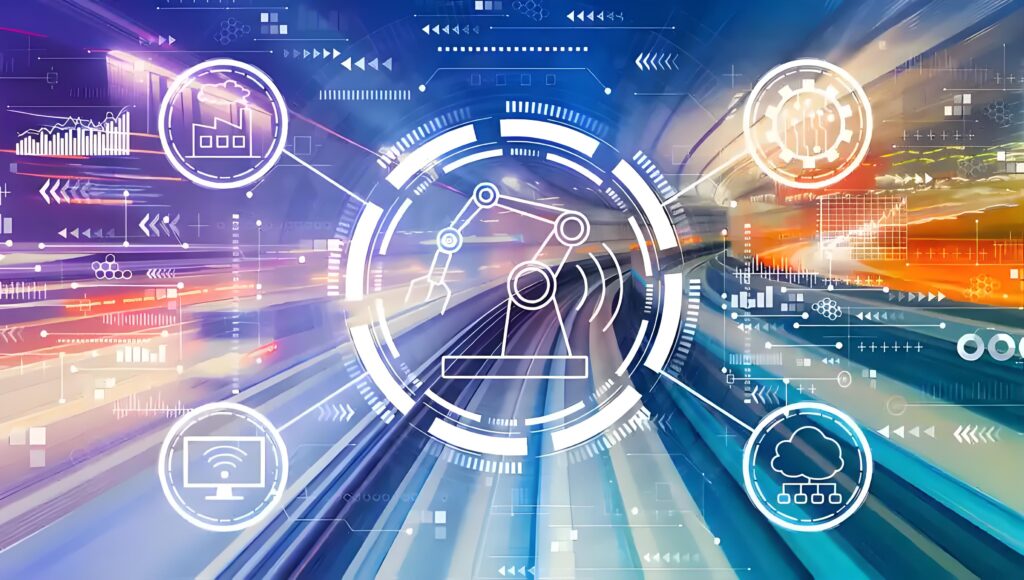
支柱 1:智能连接--智能工厂的神经系统
工业 4.0 的第一个支柱是 聪慧 连通性确保机器、人类和系统之间的无缝通信。
5G 与时间敏感型网络 (TSN)
- 超可靠通信:5G 的低延迟和高带宽可实现机械臂、AGV 和物联网传感器的实时协调。例如,在汽车装配线上,5G 可确保焊接机器人和传送带完全同步运行。
- TSN 整合:时间敏感型网络可确保为关键任务优先提供数据,如紧急关机或精密校准。
工业物联网网关
- 多协议支持:网关将传统 PLC 与现代云平台连接起来,实现 Modbus 和 MQTT 设备之间的数据流。
- RTK 定位:高精度定位系统可引导仓库中的自动叉车和无人机,最大限度地减少导航误差。
影响:工厂可实现从原材料进货到质量控制的端到端可视性,同时减少通信滞后。
支柱 2:边缘动力智能--源头大脑
第二大支柱工业 4.0 、 边缘动力智能它将计算能力直接带到工厂车间,实现即时决策。
边缘计算节点
- 实时 分析:边缘设备在本地处理传感器数据,检测电机振动或温度峰值等异常情况。在半导体制造中,这可以对蚀刻工艺进行即时调整。
- 人工智能驱动 质量控制:带有嵌入式人工智能的摄像头可检测产品缺陷,并在不依赖云的情况下标记问题。
适应性 机器学习
- 自优化系统:边缘人工智能模型从生产模式中学习,优化设备设置以提高能效。例如,注塑机可自主调节压力和温度,以减少材料浪费。
影响:工厂从被动的故障排除转变为主动的优化,从而减少停机时间和浪费。
支柱 3:数据驱动的自主--自给自足的工厂
第三根支柱 数据驱动的自治它将工厂转变为能够端到端优化的自治生态系统。
统一 AIoT 平台
- 集中式仪表板:将来自机器、ERP 系统和供应链的数据整合到一个界面中。生产经理可实时监控 OEE(整体设备效率)等关键绩效指标。
- 预测性 维护:人工智能分析历史数据,预测设备磨损情况,在故障发生前安排维修。
闭环自动化
- 自愈系统:当数控机床检测到刀具磨损时,它会自动发出更换指令并调整加工参数。
- 动态资源配置:算法根据优先级的变化重新分配能源、劳动力和材料,非常适合处理紧急订单或供应链中断。
影响:制造商实现真正的自主化,使系统自我优化,以达到质量、成本和可持续发展的目标。
应用 - 工业 4.0 在行动
汽车制造:定制化的敏捷生产
挑战:汽车工厂面临着越来越大的压力,既要提供个性化的汽车(如定制内饰、电动汽车配置),又要不降低生产速度。传统系统在频繁的重新调整和质量不一致的问题上举步维艰。
解决方案:
- 支持 5G 的灵活线路:
- 具有 RTK 定位功能的自主移动机器人 (AMR) 可在工作站之间动态导航,为定制车辆的制造提供零部件。
- 与 5G 相连的焊接机器人可根据物联网传感器提供的材料厚度数据实时调整参数。
- 边缘供电 质量保证:
- 人工智能摄像头可检测油漆表面和焊缝,并将结果与理想规格的数字双胞胎进行比较。
- 缺陷会触发抛光机器人或返工队列的自动调整。
成果:
- 在同一条生产线上实现汽油动力、混合动力和电动汽车生产之间的无缝转换。
- 降低返工成本,更快地交付定制订单。
电子组装:零缺陷微型制造
挑战:电路板或半导体芯片中的微小缺陷可能导致代价高昂的召回。传统的光学检测系统会漏掉细微的缺陷。
解决方案:
- 人工智能增强显微镜:
- Edge AI 可分析显微镜拍摄的高分辨率图像,检测出窄至几微米的焊接裂缝。
- 自学算法通过研究历史缺陷模式提高检测准确性。
- 闭环过程控制:
- 检测系统的实时反馈可调整焊接温度或元件贴装压力。
- 数字双胞胎模拟热应力对电路寿命的影响。
成果:
- 近乎完美的缺陷检测率,最大限度地减少保修索赔。
- 加速生产用于物联网设备和可穿戴设备的微型元件。
重型机械:可持续的弹性运营
挑战:金属锻造等能源密集型工艺耗电量过高,而意外停机则会打乱项目时间表。
解决方案:
- 预测能源 优化:
- 边缘分析将炉温、材料硬度和能耗联系起来,以识别浪费。
- 人工智能将高能耗任务安排在非高峰期的公用事业定价窗口。
- 自主健康管理:
- 液压机上的振动传感器可提前数周预测轴承故障。
- 自诊断数控机床通过集成供应链平台自动订购更换部件。
成果:
- 降低碳足迹,实现 ESG 目标。
- 通过基于状态的维护来延长机械的使用寿命。
制药生产:规模化合规
挑战:严格的监管要求需要完美无瑕的文档,而污染风险则威胁着批次的完整性。
解决方案:
- 区块链支持的可追溯性:
- 物联网传感器跟踪洁净室的温度、湿度和气流,将数据记录在防篡改区块链账本上。
- 自主无人机根据实时粒子计数对生产区域进行消毒。
- 人工智能驱动的合规性审计:
- 自然语言处理 (NLP) 将生产日志与 FDA/EU 法规进行交叉比对,标出不一致之处。
- 数字工作指南通过 AR 眼镜为技术人员提供指导,确保他们遵守规程。
成果:
- 加快监管审批和审计准备。
- 消除关键流程中的人为错误。
智能制造的未来
在工业 4.0 的下一阶段,这些支柱将得到更深入的整合:
- 数字双胞胎:工厂的虚拟副本可在实施前模拟生产变化。
- 协作 人工智能:全球工厂的机器共享见解,共同提高效率。
- 可持续自治:人工智能在生产目标与可再生能源使用和碳排放目标之间取得平衡。
结论
从 "制造 "到 "智造",关键在于掌握三大支柱: 智能连接, 边缘动力智能和 数据驱动的自治.通过采用这些技术,制造商可以:
- 复原力:迅速适应市场变化和干扰。
- 效率:减少浪费,最大限度地利用资源。
- 创新:通过数据支持的洞察力加快研发周期。
未来的工厂不仅是自动化的,而且是智能化的。