Industrial automation is transforming the manufacturing and production industries by enhancing efficiency, improving safety, and reducing human labor costs. With the rapid advancement of technology, businesses are increasingly adopting automation systems to optimize their operations. But what is industrial automation, and how does it work? In this blog, we will delve into the definition, types, benefits, and applications of industrial automation, as well as explore its growing role in shaping the future of industries.
Table of contents
What is Industrial Automation?
At its core, industrial automation is the application of technology to perform tasks that were once done manually. These tasks include controlling machinery, processes, and systems. The goal is to replace or assist human operators in monitoring and controlling various industrial systems, making processes faster, safer, and more efficient.
Key components of industrial automation include:
- Programmable Logic Controllers (PLCs): These are digital computers used for automation of electromechanical processes. Such as controlling machinery or production lines.
- Robotics: Automated robots perform tasks ranging from assembly to packing and even welding.
- Sensors and Actuators: These devices gather information from the physical world and carry out specific functions based on programmed logic.
- SCADA Systems: Supervisory Control and Data Acquisition systems help manage and monitor automated systems in real time.
By integrating these components, industrial automation facilitates operations that require minimal human interaction, enabling industries to run smoothly and efficiently.
Types
There are several types of industrial automation, each designed to meet different needs and requirements in manufacturing and production environments. These include:
- Fixed or Hard Automation: This type involves the use of specialized equipment and tools designed to perform specific tasks. It is ideal for mass production of standardized products and offers high production rates but limited flexibility.
- Programmable Automation: This type allows for flexibility in production, making it suitable for batch production. Programmable automation systems can be reprogrammed to accommodate different products.
- Flexible or Soft Automation: This type is highly versatile and can easily be adjusted for various products or tasks. Flexible automation systems, like robotic arms, can change the type of work they perform based on the requirements of the process.
- Industrial Robotics: These systems use robotic arms or other automated machinery to perform tasks that would be too dangerous, precise, or monotonous for human workers, such as assembly, inspection, and packaging.
The Advantages of Industrial Automation
The benefits of industrial automation are numerous, and companies worldwide are leveraging these advantages to improve their operations. Some of the key benefits include:
- Increased Efficiency: Automated systems can work 24/7 without breaks, improving production efficiency and throughput.
- Reduced Labor Costs: By automating repetitive or dangerous tasks, businesses can reduce reliance on human labor, cutting labor costs and increasing profitability.
- Improved Quality and Consistency: Automation ensures high levels of precision, reducing human errors and ensuring uniformity in products.
- Enhanced Safety: Automated systems can handle hazardous or physically demanding tasks, minimizing the risk of accidents and injuries in the workplace.
- Better Resource Management: With automated processes, industries can reduce waste, optimize energy consumption, and enhance overall resource management.
Where is Industrial Automation Used?
Industrial automation is employed across a wide range of industries and sectors. Some of the key areas where automation plays a pivotal role include:
- Manufacturing: Automation is heavily used in automotive, electronics, and food and beverage industries for tasks like assembly, packaging, and quality control.
- Oil and Gas: Automation is used to monitor and control production processes, ensuring the safe and efficient extraction of oil and gas.
- Pharmaceuticals: Automated systems are crucial for precise and controlled manufacturing processes, such as packaging and labelling.
- Warehousing and Distribution: In warehouses, automated guided vehicles (AGVs) and robotic arms help with sorting, picking, and packing.
- Agriculture: Automation in agriculture includes the use of drones, automated tractors, and irrigation systems to optimize farming practices.
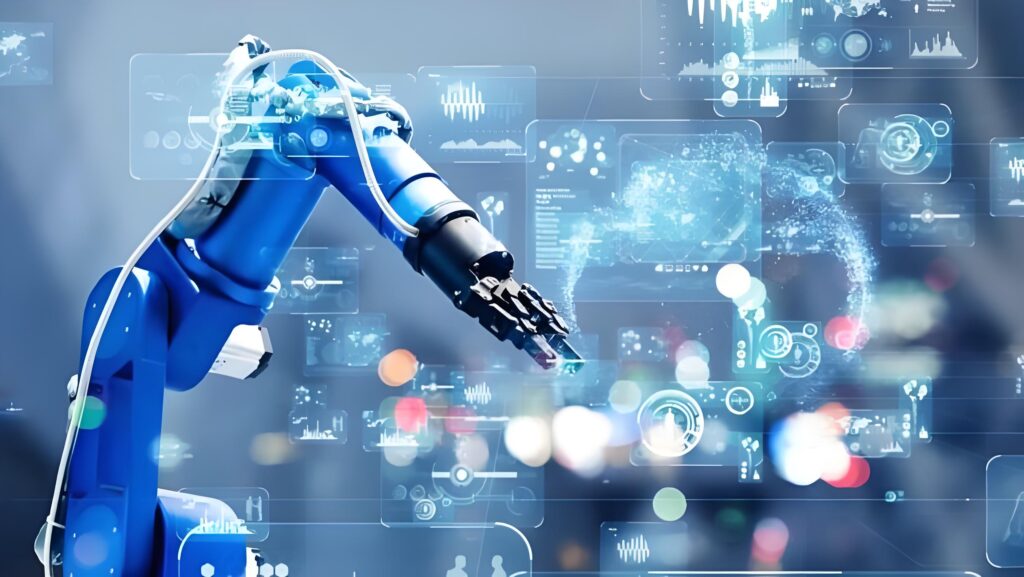
Why is Industrial Automation Growing?
The adoption of it is accelerating due to several factors:
- Technological Advancements: The development of IoT (Internet of Things), AI (artificial intelligence), and machine learning has made automation systems smarter and more capable.
- Cost-Effectiveness: As the cost of automation technology decreases, more businesses can afford to implement automated systems.
- Globalization: The need for faster production and global supply chains has driven the demand for automation.
- Labor Shortages: In industries where skilled labor is in short supply, automation helps fill the gap and ensures continuity in production.
- Sustainability: Automation systems can optimize resource usage, reduce waste, and lower environmental impacts. Which making them an attractive solution for sustainable manufacturing.
Future
The future of industrial automation looks promising, driven by innovations in AI, robotics, and IoT. Some of the key trends expected to shape the future include:
- Industry 4.0: This refers to the integration of smart technologies such as IoT, AI, and big data with traditional manufacturing systems. Industry 4.0 promises to bring even more automation and flexibility to industrial processes.
- AI and Machine Learning: By integrating AI into automation, machines can learn from data, optimize processes, and predict potential issues, offering even greater efficiency.
- Collaborative Robots (Cobots): Cobots will work alongside human workers, performing tasks that complement human capabilities and improving overall productivity.
- 5G Connectivity: With faster data transmission, 5G will enable real-time communication and remote control of automated systems.
Frequently Asked Questions About Industrial Automation (FAQs)
Yes, the Controller Area Network (CAN bus) is commonly used in industrial automation to enable communication between various devices such as sensors, PLCs, and actuators.
A Programmable Logic Controller (PLC) is a rugged, industrial computer used to automate processes such as controlling machinery or managing data in real-time.
A PLC is a key component of industrial automation. While it refers to the overall process of automating tasks, a PLC is specifically used to control and manage the operations within automated systems.
The three major systems in industrial automation are:
Programmable Logic Controllers (PLCs) for process control.
Supervisory Control and Data Acquisition (SCADA) for monitoring systems.
Human-Machine Interfaces (HMIs) for interaction between operators and machines.
Industry 4.0 refers to the fourth industrial revolution, which integrates cyber-physical systems, the Internet of Things (IoT), and cloud computing with manufacturing systems for increased automation, data exchange, and real-time decision-making.