Substation inspection is a cornerstone of reliable power distribution, ensuring the safety and efficiency of electrical grids. However, traditional methods, which often rely on manual checks or semi-autonomous robots with limited navigation capabilities, struggle to keep pace with the demands of modern energy systems. Enter RTK (Real-Time Kinematic) high precision positioning technology — a game-changer for substation inspection robots. By delivering centimeter-level accuracy, RTK empowers robots to navigate complex substation environments autonomously, detect faults proactively, and operate safely alongside high-voltage equipment.
This blog explores how RTK positioning transforms substation inspection, enabling utilities to achieve unprecedented levels of safety, accuracy, and operational efficiency.
Table of contents
The Challenges of Traditional Substation Inspection
Substations are dense with transformers, circuit breakers, and power lines, creating a high-risk environment for human workers and conventional robots. Key challenges include:
- Navigation Hazards: Narrow pathways, elevated platforms, and live equipment demand precise movement to avoid collisions.
- Data Accuracy Gaps: Manual inspections may miss subtle defects like corroded connectors or insulation cracks.
- Operational Downtime: Frequent shutdowns for inspections disrupt power supply and increase costs.
- Safety Risks: Human exposure to high-voltage zones remains a critical concern.
These challenges underscore the need for smarter, more adaptive inspection solutions.
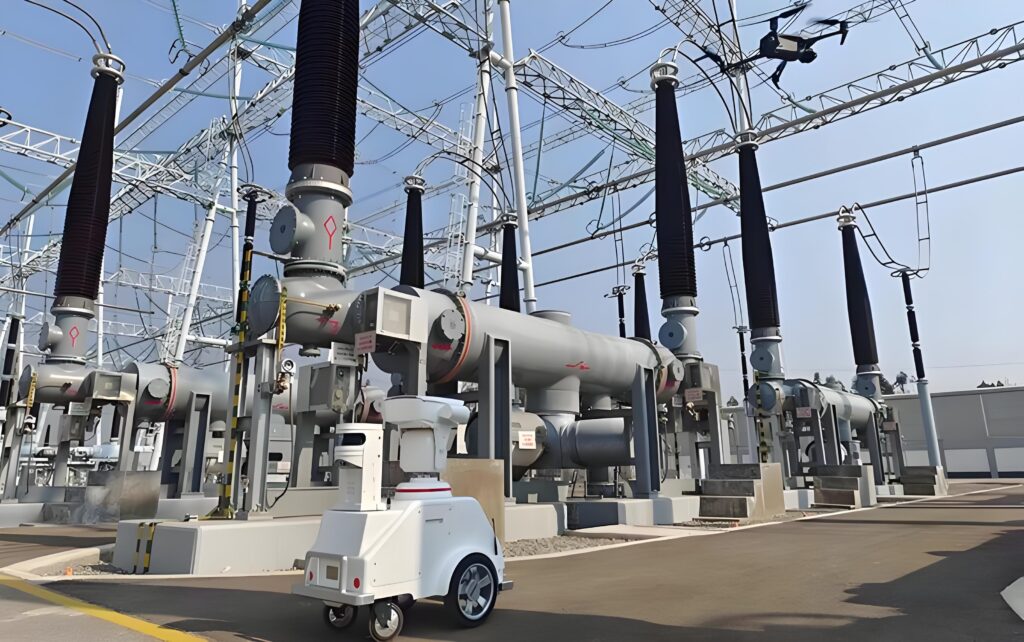
RTK Positioning: Precision Meets Substation Safety
RTK technology enhances GNSS (Global Navigation Satellite System) data by correcting signal errors in real time, achieving centimeter-level positioning accuracy. Consequently, for substation inspection robots, this precision is transformative.
How RTK Works in Substations
- Base Station Corrections: A fixed RTK base station within or near the substation calculates satellite signal errors caused by atmospheric interference.
- Real-Time Data Transmission: Corrections are sent via 5G or dedicated radio to inspection robots, ensuring uninterrupted accuracy.
- Multi-Sensor Fusion: RTK data combines with lidar, cameras, and inertial sensors to create robust navigation in GPS-denied areas (e.g., under steel structures).
Key Advantages for Substation Robots
- Autonomous Navigation: Robots follow predefined paths with minimal deviation, avoiding collisions with critical infrastructure.
- Fault Detection Precision: Accurate positioning ensures thermal cameras and sensors align perfectly with equipment for reliable diagnostics.
- 24/7 Readiness: Robots operate in harsh weather or low-light conditions, reducing dependency on human schedules.
Integrating RTK into Substation Inspection Solutions
Deploying RTK-powered robots requires a holistic approach:
- Weatherproof Design: Substation robots operate in rain, snow, and extreme temperatures. RTK receivers must withstand these conditions.
- Anti-Interference Shielding: Protection against electromagnetic interference from high-voltage equipment.
- Intelligent Navigation Software
- Dynamic Path Planning: Adjust routes in real time to avoid unexpected obstacles (e.g., maintenance vehicles).
- Zone-Based Speed Control: Slow down near sensitive equipment or accelerate in open areas to optimize inspection cycles.
- Data Integration Platforms
- Centralized Dashboards: Visualize robot paths, inspection results, and equipment health metrics in real time.
- Predictive Analytics: Flag deteriorating assets (e.g., overheating transformers) before failures occur.
Applications: RTK-Powered Robots in Action
- Thermal Imaging Inspections
- Challenge: Detecting overheating components in cluttered substations.
- Solution:
- RTK guides robots to predefined hotspots (e.g., circuit breaker contacts).
- Thermal cameras capture precise temperature data, with positioning accuracy ensuring no component is missed.
- Outcome: Early detection of potential failures, preventing unplanned outages.
- Equipment Condition Monitoring
- Challenge: Inspecting hard-to-reach areas like transformer bushings.
- Solution:
- Robots navigate narrow walkways and staircases using RTK waypoints.
- High-resolution cameras and ultrasonic sensors assess equipment integrity.
- Outcome: Comprehensive inspections without requiring scaffolding or human entry.
- Emergency Response
- Challenge: Assessing damage after storms or equipment failures.
- Solution:
- RTK-enabled robots map damaged zones and prioritize hazards (e.g., downed power lines).
- Live video feeds guide repair crews safely.
- Outcome: Faster, safer restoration of power.
Why Utilities Choose RTK-Based Solutions
Utilities worldwide are increasingly adopting RTK (Real-Time Kinematic) positioning technology to modernize substation inspection processes. Here’s why this approach aligns perfectly with their operational priorities:
- Safety First: Protecting Personnel and Assets Substations are high-risk environments filled with live electrical equipment, elevated structures, and confined spaces. RTK-powered inspection robots remove the need for human workers to enter these hazardous zones, significantly reducing exposure to accidents. With centimeter-level positioning accuracy, robots navigate precisely around sensitive infrastructure, avoiding collisions with transformers, circuit breakers, or power lines. This ensures both worker safety and equipment integrity, while enabling round-the-clock inspections in adverse weather or low-light conditions.
- Cost Efficiency: Streamlining Operations Manual inspections often require costly substation shutdowns and large teams to cover expansive facilities. However, RTK-based robots eliminate these inefficiencies by automating repetitive tasks. They operate during normal grid activity, avoiding revenue losses from downtime, and reduce reliance on specialized labor. Over time, the combination of predictive maintenance (enabled by precise data collection) and lower labor costs delivers measurable financial benefits, making inspections both faster and more economical.
- Regulatory Compliance: Ensuring Accountability Power providers must adhere to strict grid reliability and safety standards. RTK technology supports compliance by generating accurate, auditable inspection records. Moreover, every robot-guided inspection is geotagged and time-stamped, providing irrefutable proof that critical components like insulators, bushings, or grounding systems were thoroughly assessed. This transparency simplifies audits and helps utilities meet evolving regulations, such as environmental mandates for leak detection or vegetation management.
- Scalability: Adapting to Diverse Needs Whether managing urban substations with complex layouts or remote sites with limited connectivity, RTK delivers consistent performance. The technology integrates seamlessly with existing infrastructure, requiring no costly overhauls. Utilities can deploy robots across multiple locations simultaneously, using centralized platforms to monitor progress and prioritize maintenance. This scalability future-proofs operations, allowing easy adoption of upgrades like AI analytics or 5G connectivity as grids evolve.
The Future of Substation Inspection
As grids modernize, RTK technology will play an even greater role:
- AI-Driven Autonomy: Robots will predict and adapt to equipment degradation patterns.
- 5G Integration: Ultra-low latency communication enhances real-time control.
- Swarm Robotics: Teams of RTK-synchronized robots inspect large substations collaboratively.
Conclusion
Substation inspection is evolving from a risky, labor-intensive task to a precise, automated process—thanks to RTK positioning. As a result, by enabling robots to navigate with unmatched accuracy and reliability, utilities can safeguard their infrastructure, optimize maintenance, and deliver uninterrupted power to communities.