The advent of the Internet of Things (IoT) has revolutionized multiple industries, and one of the most significant transformations is occurring in the realm of Industry 4.0. Industry 4.0, often referred to as the Fourth Industrial Revolution, is marked by the integration of digital technologies into manufacturing processes. At the heart of this transformation is IoT, which is driving efficiency, improving decision-making, and enabling automation across industrial sectors. In this blog, we will explore how IoT is driving Industry 4.0, the impact it has on businesses, and the various challenges and opportunities it brings.
Table of contents
What is Industry 4.0?
Industry 4.0 refers to the fourth phase of industrial development, which builds on the digitization of manufacturing processes. It integrates cyber-physical systems, automation, big data, AI, IoT, and cloud computing into the traditional manufacturing and industrial setup. The goal of Industry 4.0 is to create intelligent factories that are more efficient, flexible, and sustainable.
In Industry 4.0, machines communicate with each other in real-time, collecting and sharing data that can be used for predictive maintenance, supply chain optimization, and decision-making. Through automation, real-time monitoring, and data-driven insights, companies can not only enhance their productivity but also improve the quality and speed of their products and services.
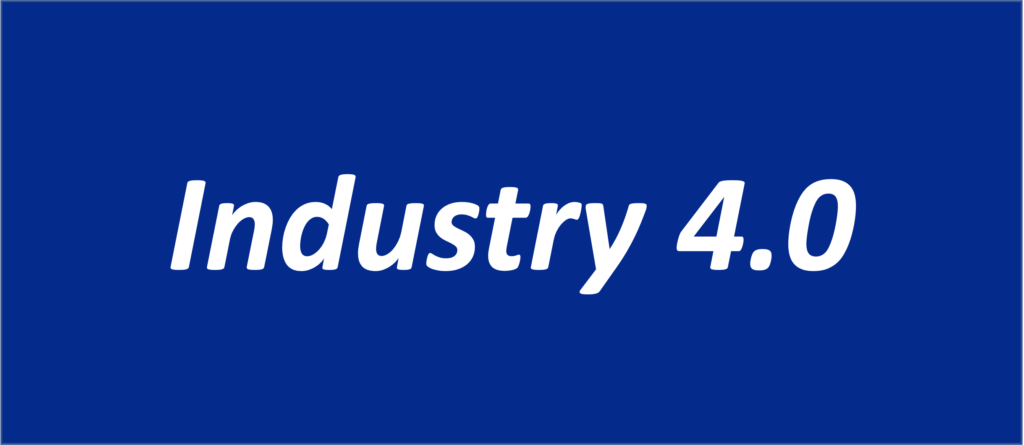
How is IoT Driving Industry 4.0?
When we talk about IoT driving Industry 4.0, we’re referring to the way in which connected devices, sensors, and machines are enabling the seamless exchange of data across an entire production ecosystem. These IoT-enabled devices collect valuable information that drives informed decision-making, predictive analysis, and operational improvements.
Here are some key ways in which IoT is driving Industry 4.0:
- Automation and Efficiency: IoT enables machines to communicate and work together without human intervention. Automation tools powered by IoT sensors improve workflow efficiency, reduce errors, and speed up production timelines.
- Predictive Maintenance: IoT devices monitor equipment in real-time, providing insights into performance. This allows manufacturers to predict when machines will need maintenance, reducing downtime and avoiding costly repairs.
- Data-Driven Decision Making: With IoT, businesses can collect massive amounts of data from sensors, devices, and machines. This data is processed and analyzed, providing actionable insights that can optimize production, inventory management, and other business operations.
- Supply Chain Optimization: IoT helps track products and raw materials throughout the supply chain, providing real-time visibility. This enables manufacturers to respond faster to demand changes, manage inventories more effectively, and reduce waste.
- Smart Manufacturing: IoT allows for the creation of smart factories that can adapt to changing conditions, optimize energy use, and improve worker safety. The integration of IoT in production lines leads to a more efficient and streamlined manufacturing process.
What is the Impact of IoT in Industry 4.0?
The impact of IoT in Industry 4.0 is profound and far-reaching. It transforms how businesses operate, make decisions, and deliver value. Here are some key areas where IoT is making a major impact:
- Improved Operational Efficiency: IoT-enabled sensors and devices ensure that every part of the production process is optimized, from monitoring machinery health to automating production workflows. This leads to reduced operational costs and more efficient resource management.
- Enhanced Product Quality: Real-time monitoring through IoT devices ensures consistent quality by detecting defects or inefficiencies early in the process. With IoT, manufacturers can quickly identify and address issues, leading to higher-quality products.
- Faster Time-to-Market: IoT-driven automation helps reduce lead times by streamlining production and improving supply chain management. As a result, companies can deliver products faster to meet customer demands.
- Cost Reduction: By improving efficiency, reducing downtime, and enabling predictive maintenance, IoT lowers operational costs. Additionally, the ability to track and monitor resources in real time helps avoid overproduction, reducing waste and excess costs.
The Use Cases of IoT Working in Industry 4.0
IoT driving Industry 4.0 is not just a theoretical concept but a real-world implementation with tangible results. Below are some common use cases where IoT is playing a crucial role in Industry 4.0:
- Predictive Maintenance: IoT sensors on industrial machinery monitor equipment in real-time to detect wear and tear. This allows companies to schedule maintenance before equipment breaks down, avoiding costly repairs and minimizing downtime.
- Smart Manufacturing: IoT devices in production lines enable the automation of tasks such as assembly, packaging, and testing. These systems can adjust production schedules and workflows based on real-time data, ensuring maximum efficiency.
- Supply Chain Management: IoT tracks products, raw materials, and shipments as they move through the supply chain. Companies can monitor inventory levels, optimize shipping routes, and manage supply chain disruptions in real-time.
- Energy Management: IoT sensors help monitor energy consumption in manufacturing facilities. By analyzing this data, companies can reduce energy use, minimize waste, and optimize resource allocation, contributing to sustainability goals.
- Worker Safety: IoT devices, such as wearable sensors, help monitor the safety of workers in hazardous environments. These sensors can detect hazardous gases, extreme temperatures, or sudden falls, sending alerts to ensure timely intervention.
What Challenges Does IoT in Industry 4.0 Face?
While IoT in industrial automation offers substantial benefits, it also presents several challenges:
- Cybersecurity Risks: With the vast amount of data being transferred across devices and systems, security becomes a major concern. Ensuring that sensitive data is protected from cyber-attacks is critical to the success of IoT in Industry 4.0.
- Data Overload: IoT generates massive amounts of data. Managing, processing, and making sense of this data can be overwhelming, especially for smaller organizations with limited resources.
- Integration with Legacy Systems: Many industries still rely on legacy systems that were not designed to accommodate IoT technologies. Integrating IoT devices with these systems can be complex and costly.
- High Initial Investment: The costs of implementing IoT devices, sensors, and automation systems can be significant. For small and medium-sized enterprises (SMEs), this can be a major barrier to adoption.
Frequently Asked Questions About IoT and Industry 4.0 (FAQs)
Embedded IoT refers to IoT devices that are integrated directly into machines or equipment in a manufacturing environment. These embedded devices collect data and perform specific tasks, such as monitoring temperature or pressure, without the need for external sensors.
Data security is a critical concern in Industry 4.0. With proper encryption, cybersecurity protocols, and secure communication channels, businesses can protect their data and customer information while leveraging IoT technologies.
Yes, it is possible to integrate IoT into existing systems, but it may require some adjustments. Retrofitting legacy systems with IoT sensors and software can help businesses take advantage of Industry 4.0 benefits without a complete overhaul of infrastructure.
IoT plays a central role in Industry 4.0 by connecting devices, sensors, and machines to collect, analyze, and share data in real-time. This enables automation, predictive maintenance, and smarter decision-making across the industrial sector.
Some security risks include unauthorized access to IoT devices, data breaches, and cyber-attacks on industrial systems. It’s crucial to implement robust security measures to protect devices and data.
To improve IoT security, businesses should use encryption, multi-factor authentication, secure communication protocols, and regular software updates to protect devices and networks from vulnerabilities.